
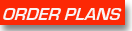
Reduced Price $75
Plans are now shipping and they are beautiful
Click for a sample of the MEG-2X Drawings
The dream of personal flight
goes back to Icarus, the mythical character who made wings of wax and feathers, then
soared too close to the sun. Today the vision is lived out in modern form with machines
such as flying platforms, rocket propulsion backpacks, and fixed-wing ultralight aircraft.
But the idea of a VTOL machine - a personal ultralight helicopter - holds a special fascination for
those of us who are smitten.
When Eugene M. Gluhareff
examined the technical challenges of personal flight from his
perspective as a helicopter design engineer, it quickly became obvious
that the absence of a suitable blade-tip powerplant was the missing
ingredient. So he designed his own powerplant specifically for this type
of application. Today's pressure jet engine is the result of some 30
years of refinement. And you can build the engine yourself following the
step-by-step instructions in our comprehensive plans package.
Simple Design
The simple design of the Gluhareff Pressure Jet engine is one of the reasons for its huge popularity. The jet is a remarkably simple device made of thin-wall
stainless steel tubing and sheet metal. Inside, it contains only a length of coiled steel
tubing (the fuel line), which gasifies and super-heats the incoming liquid propane before
it is injected at supersonic speed at the top of the intake stack. The engine has no
moving parts, yet it is fully throttleable.
One of the most remarkable aspects of the engine is that it works at all. Prior to Mr.
Gluhareff's design, engineers had understood that it was possible to produce thrust by
using the energy of pressurized propane to induce the fuel/air mixture. Calculations,
however, indicated a maximum thrust of less than 10 pounds, and extremely high
specific fuel consumption (fuel consumed per unit of power output). The secret to the
success of the Gluhareff Pressure Jet is its sonically tuned intake stack, which results
in far greater thrust and far lower specific fuel consumption.
Three intake stages are sized according to the length of the sound waves produced when
the engine is running. The sound waves act against the intake stack to create a
pumping action that pressurizes the incoming fuel/air mixture. If the intakes are not in
tune, the small 20-lb thrust engine, for example, produces less than ten pounds of
thrust. The fish-mouth cut at the rear of the tailpipe reduces noise and increases thrust.
Building the jet requires some sheet metal forming, but much of it can be assembled from
stock materials. For example, the exhaust pipe, combustion chamber, and fuel lines are cut
from thin-wall stainless steel tubing. The intake stages, the diffuser skirt that
blends the final intake stage into the combustion chamber, and the transition piece
between the combustion chamber and the exhaust pipe are hand formed. You can spin the nose
cone on an ordinary home workshop woodworking lathe. By doing the fabricating and welding yourself, total building
costs can be held to little more than the cost of the sheet metal, tubing, and fittings.
Specifications
Engine |
G8-2-20 |
G8-2-40 |
G8-2-80 |
G8-2-130 |
Length
(inches/mm) |
36/914.4 |
38.5/978 |
45/1143 |
48/1219 |
Intake to CL
Burner
(inches/mm) |
25.5/647.7 |
27.5/698.5 |
36/914.4 |
37/939.8 |
Weight
(lbs/kg) |
5.5/2.5 |
5.5/2.5 |
21/9.53 |
21/9.53 |
SFC Static
(lbs fuel per lb thrust per hour) |
4.8 |
4.6 |
4.6 |
*1.33/0.77 |
SFC Dynamic**
(lbs fuel per lb thrust per hour) |
*1.33/0.77 |
N/A |
N/A |
N/A |
*Oval intake/round intake
**With ram air intake, SFC declines with increased speed. SFC at 293 ft/sec (89.4 m/sec)
is approximately 1/3 of static value. |
About The Inventor
Eugene M. Gluhareff was a graduate Aeronautical Engineer from the Rensselaer
Polytechnic Institute in Troy, New York. He was a key figure in the history of the
helicopter almost from its inception, working directly under Igor I. Sikorsky and
side-by-side with Igor A. Sikorsky, Chief of Aeronautics at Sikorsky Aircraft Corp.
In addition to producing many conventional helicopter designs, he also pioneered the
single-bladed rotor system, and invented the Kerosene Fueled Valveless Pulse Jet engine,
which was used to power the world's first single-bladed one-man helicopter (also of his
design). Later he developed a Delta-Wing Convertiplane for the USAF, which utilized a
foldable single-blade rotor with a blade-tip cold-jet power system. He was Project
Engineer on the Top Sergeant pulse-jet powered helicopter, and developed the XH-26 one-man
tip jet powered helicopter for the USAF.
In the early 1960's, Mr. Gluhareff developed rotary wing drones for the U.S. Navy. After
joining Douglas Aircraft Co. in 1963, he worked as Design Engineer Scientist on the Saturn
Rocket and was in charge of the sequence of events from firing to parking orbit on
subsequent launchings. Following the Saturn program, he became Specialist in the design of
Rocket Stabilization Systems for ejection seats and space capsules.
In 1972, he established EMG Engineering in Gardena, California, where he continued the
development of the propane-fueled pressure jet engine featured here. Building this
remarkable jet engine will be a gratifying and inexpensive way of owning an important piece of
aviation history.
About the Plans
This plan-set is based on Mr. Gluhareff's original drawings, technical documents,
hand-written construction notes, and photographs. Engineering/theoretical information in the
manual was taken from the Technical Handbook provided by Mr. Gluhareff with the GTS-15
Teaching Stand, which has been used by universities to teach the principles of jet engine
operation. The step-by-step construction procedures in the manual, which runs in a web browser, were
derived from Mr. Gluhareff's professional notes and drawings on the various procedures
used to hand-build engines in his workshop. Previously unpublished photographs in the manual let you look over the shoulders of one of Mr. Gluhareff's craftsmen and see the engine at various stages of construction as it's being assembled.
Conventional 2D drawings are included in both PDF and CAD formats. IGES files on the disc give your machinist the the ability to make quick work of the injection nozzle. Native 3D files allow for importing.
With this plan-set, you receive the only authorized
and updated work available of Mr. Gluhareff's designs. Complete plans are provided on CD-ROM. The CD-ROM runs in a web browser and you navigate just like you would navigate through a website on the Internet. Links to online vendors and videos are provided on the disc. If desired you can print the 2D drawings from the PDF files on disc, or you can order a complete set of 19 D-size drawings with your CD-ROM, or you can return and order prints later on.
The Printed Plans Option on the Order Form
The Bonus plans for the 5-lb jet and the MEG-2X backpack helicopter are available only on CD-ROM in electronic format. If desired, the 2D drawings on the disc can be printed by a local service. If you select the option on the order form to include printed plans, you will receive 19 D-size drawings, which will include all four thrust-sizes of the jet. This set of prints, however, will not include drawings of the MEG-2X and the 5-lb jet. Those drawings can be printed from the disc. |
Bonuses You Will Receive
You will receive two bonuses with your new plan-set on disc; an easy-to-build 5-lb thrust engine for desktop demonstration and plans for the MEG-2X experimental backpack helicopter. Both of these items have been modeled in 3D CAD. Neither of these plan-sets have been offered before now. As an aid to those that would like to experiment with ultralight helicopters, the disc includes links to 13 in-depth seminars on helicopter aerodynamics, design, and operation. Although the plans are mainly about the pressure jet engine itself, rotary wing enthusiasts will find the package a virtual gold mine of information. 3D CAD models and drawings can be viewed on your computer without having to purchase the native software. The viewer lets you rotate, pan, make section views, take dimensions, and make parts transparent so you can see what's underneath. It creates a whole new depth of understanding how the items are built and how they work.
A Powerful Teaching Aid
There is nothing like the 3D CAD experience to get youngsters motivated about the computer aided design and the engineering professions. And there is nothing as effective as these modern technologies to assist in the actual building process. The educational community calls it “project-based learning”, and it's a powerful way to engage participants - professors and students alike. If you want to spark enthusiasm in a youngster, work with him or her in building an exciting and serious project like a jet engine. It will absolutely transform the impact of the experience, and you will be teaching things you may not even know you are teaching - project management and funding, computer aided design, the relationship of effort to reward, as well as actual mechanical and fabrication skills. And as a DIY enthusiast, it will transform your experience as well. You will learn things like the relation of thrust to the fuel's energy and the design of the engine, and how a reaction motor's thrust translates into horsepower or kilowatts. Universities have used the G8-2 jet to teach physics because it captivates students' interest, and it serves as a simple model for the physics of converting fuel into power. Details and equations are in the manual on disc. Click on the image to the right to see a sample page taken from the beginning of the technical discussion in the manual. (If the large image is unclear, your browser may have resized it to fit your monitor. Displaying it full size will give better results.)
Cory Waxman, a professor at Bioscience High School in Phoenix, has created a school-wide sustainable transportation program around our XR3 Hybrid three-wheeled vehicle. Click on the following link for a brief article by Mr. Waxman on how this hands-on project is transforming the learning experience for students: Project Based Learning
Although it uses the XR3 Hybrid as an example, and certain features may not apply to this project (like decals and the ability to do 3D printing), here's a general overview of our CAD-based plan-sets: Advanced CAD-based plan-sets. For this presentation, the 5-lb jet and MEG-2X helicopter were done in Solidworks. The other jets, 20-lb through 130-lb, were done in Rhino. Native files are on the disc, plus in a format that can be viewed on your computer with a free viewer, without having the native CAD program.
|